Companies using the DLC coating process have seen many beneficial things happen for their businesses, such as increased savings and lowered maintenance tasks. Your business’s production could also improve by using a DLC coating process. Continue reading to learn the overview of the DLC coating process and why it’s important.
Why Is the DLC Coating Process Important?
DLC is a special type of coating that enhances the mechanical parts of machines, ensuring they don’t deteriorate from corrosion. When the vapor sprays onto the surface, less friction occurs. After using DLC, objects and machine parts look better; the finish gives a grandeur luster that’s hard to look away from!
Applying a DLC coating is a multiple-step process that doesn’t cut corners when creating an environmentally friendly workstation and reducing corrosion. This advanced process can carry a significant price tag, but it is worth it. Start looking into the steps of the DLC coating process yourself if you want something that lasts a long time and doesn’t require too much maintenance later.
What Are the Steps of the DLC Coating Process?
You’re likely looking at your options now in order to find the right DLC coating option for your company’s production processes. Understandably, your current machines will break down, but why could that be? Over time, machinery parts tend to rust, and the machine’s mechanisms falter, causing power outages or accidental fires.
It is beneficial to learn the steps that go into the coating process before you invest in it. These steps are crucial to ensuring the DLC coating method is effective. If you experience issues during the coating process, you may need to bring in extra assistance from trained professionals.
The Precleaning Phase
Before you start the process, you must clean all metal surfaces. From there, workers will place the metal objects onto a rotating axis fixture—most can fit up to three pieces of metal. After placement, the fixture moves into a vacuum chamber. The vacuum turns on and works to its pre-set level.
Preheating Before Ion Bombardment
Once the vacuum hits its pre-set level, the preheating begins. After preheating, argon gas ions barrage the metal surfaces. The ions remove micro-oxides and micro-contamination, improving the face so that substrates adhere to it better.
Depositing Underlayers
DLC doesn’t go on yet; you need underlayers first. The underlayer deposition includes a layer of PVD and several other materials. The underlayer of high-density PVD goes on to create a smooth layer. Note that the substrates you use may vary.
Your layers depend on load-carrying capacity, friction, wear and contact modes, and adhesion requirements. These factors may limit your underlayers, so you must determine your needs before picking substrates.
After placing the substrates on the metal, depositing the amorphous carbon DLC layer is next. Companies can tailor the DLC layer to their specifications, such as what alloys to use if changing the DLC layers architecture or using different deposition technologies.
The amorphous layer is thick and spreads fast. The beneficial coefficiencies the layer delivers are higher hardness and less friction. The DLC coating process concludes with a cooling period. The period lasts anywhere from 12 to 24 hours.
Reasons To Use the DLC Coating Process
The DLC is essential, but you need more than an overview of the coating process to see why it’s important. These reasons to use DLC should convince you that this is the right finishing treatment for your business.
Abrasion- and Scratch-Resistant
One area where companies struggle the most when manufacturing a product or using rapid manufacturing processes is scratch and abrasion resistance. Machines break down fast when companies use quick techniques to produce as many products as possible, putting quality at serious risk.
If mass production is a long-term goal for your company, protecting your production process from abrasion and scratched surfaces are essential. Instead of sacrificing quality while making products, improve the machines you use to assemble these items first with a DLC layer. DLC has alloys that protect the surface from scratches and rust.
Creates a Unique Appearance
Every product you create doesn’t need to be an exact replica. There doesn’t need to be a set of twins or triplet car parts or home accessories, but there could be ones with similar designs. You can easily adjust your coating capabilities to your specifications when you have improved coating capabilities.
Say you create a medical cart for emergency room workers. The trolleys you make shouldn’t all look the same. Some might be useful for nurses that go through each room to examine patients, and others might work well for delivering trays of food from the hospital cafeteria.
DLC layers come in many hues, most commonly black. Businesses choosing DLC have creative liberty over their production process thanks to the flexibility of DLC layer compositions.
DLC Is Biocompatible
Most companies strive to be environmentally friendly. That is an easy goal to set, and reaching it can be affordable too. DLC might come up at a high cost, but the benefit of being a cleaner, non-toxic coating process makes it preferable over other techniques that use harmful chemicals.
ArmorLube Offers DLC Coating
The chance to improve your production process isn’t fading, but we want your business to experience the benefits of using DLC as soon as possible. ArmorLube offers DLC coating to clients to help them enhance their company and reduce time lost to repairing and replacing worn-down equipment. Our team is highly skilled and trained in DLC coating. Our industrial coating systems meet OSHA safety standards, making it a completely harmless technique with various rewarding benefits.
Learning about a process that you’re unsure of using can initially seem intimidating. We can answer all your questions about the DLC coating process and why it’s essential to use it in your production process. We want you to feel confident in your decision; our customer service representatives are ready to talk about the DLC coating process and what it can do for your company. Contact us today for a free consultation with one of our coating experts.
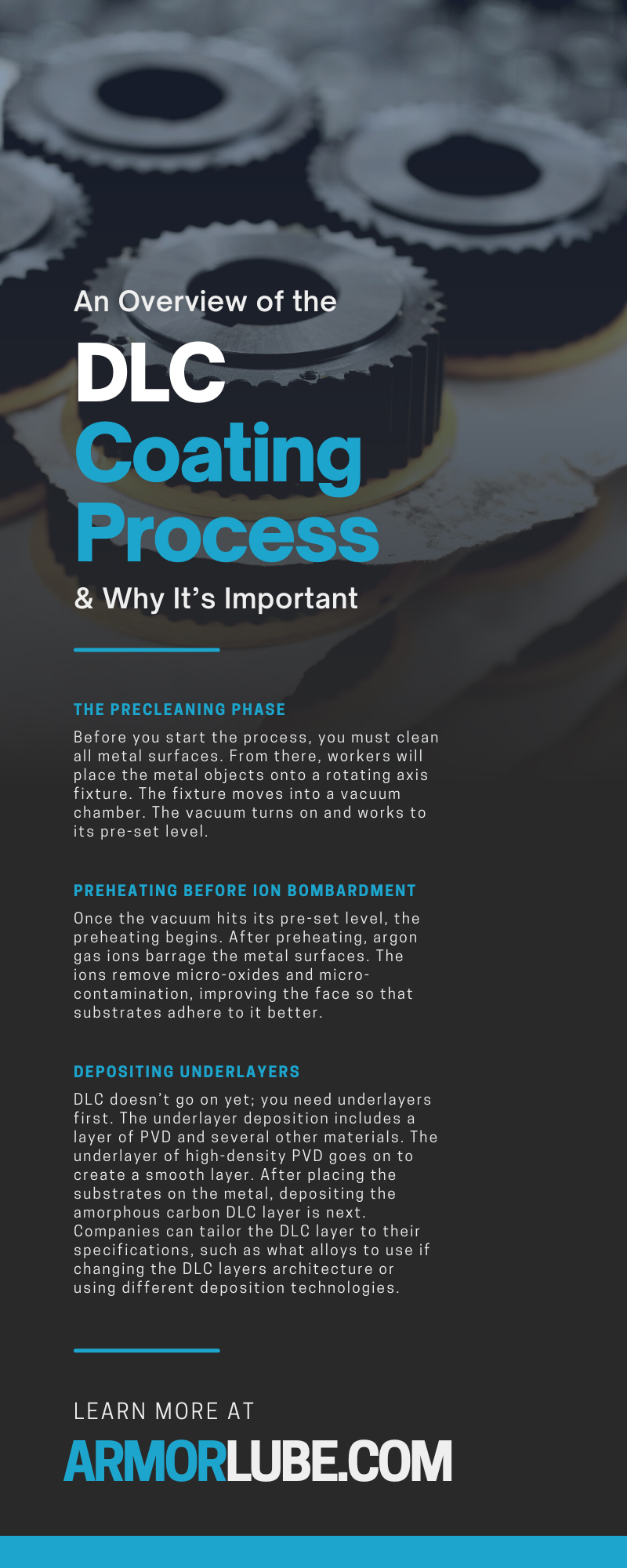