If you want your industrial equipment to last, you should use a protective coating. This special coating helps prevent and slow down common damage to industrial equipment, making it essential to increase the lifespan and enhance the performance of your equipment. Read on to learn about the benefits of using protective coating on industrial equipment.
Different Coatings Offer Different Benefits
Using a protective coating can prevent or slow the damage from a range of factors, such as water and rust. You have all kinds of protective sealants to pick from, including epoxy and powdered coatings, and the best one for you is based on your needs. But what does each do for you, and which is better?
Epoxy
Epoxy coating is related to resin—it’s a glossy, translucent base that hardens around surfaces to prevent corrosion and moisture buildup. While you can remove it easily, it becomes slippery when wet. Despite that, it could be the best option if you need to seal steel pipes and concrete floors.
Powdered Coating
Powdered coating is a good option for every industry. It’s clean, safe to use, and doesn’t cost a ton to use, adding flexibility in production. Industries that deal with heavy machinery will likely find powdered coating useful because of its strength and capability to extend a machine’s lifespan.
Common Factors Coatings Protect Against
A manufacturing workplace is full of environmental hazards that can cause harm to your equipment. However, protective coatings can stop this damage from taking place, especially damage from weather and heat. Here’s a breakdown of each:
Coatings are Weather Resistant
Weather resistance is among the most essential qualities of protective coatings. Oftentimes, the natural elements can wreak havoc on your warehouse production equipment.
Moisture damage and UV damage are common weather-related issues that protective coatings can prevent. Using a protective coating, your equipment is also safer from rust, rainwater, and ice buildup.
Coatings Have Thermal Protection
Machines can easily overheat in every workplace, but you can limit this risk with protective coatings. The coating provides temperature regulation, thereby decreasing the possibility of fires starting in your equipment.
So long as your equipment is thoroughly coated, it should receive prime protection from weather- and heat-related damage.
Coatings Add to Equipment Aesthetic
Protective coatings save your equipment and look good while doing it. Having nice-looking equipment makes your warehouse look better and adds to the professional atmosphere, making protective coatings a quality investment.
The following are common protective coating finishes and how to achieve them:
Glittery
The glittery coating can be achieved in two ways: through dry blending and bonding. The dry blending process consists of mixing a powder coating and effect pigment together to create a glitter powder. This method has benefits such as faster application and less product needed.
The other process is bonding. Bonding takes a few extra steps, but it’s more effective than dry blending since it applies more easily. It’s made by heating up powder coatings with friction, thereby creating a sticky powder.
Glossy
In order to achieve a full or semi-glossy finish, resin and other additives join the mix. When light hits the coated machine’s surface, the paint’s film absorbs and transmits the light.
When adding resin to the coating mixture, you must also include additives that help the resin that would otherwise be gummy smooth out. Once the additives are in, they also prevent moisture while providing a gentle glow to the machine.
Protective Coatings Save Money
While you may spend money on the coating and application process, protective coatings save your company money in the long run by preventing and reducing damage. As a company owner, you are aware of how expensive and time-consuming repairs and replacements can be. So if you are looking for easy ways to reduce costs, investing in protective coating is a great way to start. After applying a coating, your machines last longer, so they will require less maintenance and fewer repairs.
Protective Finishes Increase Resale Value
At some point, you may want to sell your equipment to downsize or upgrade. However, if your equipment is damaged, then so is its value. Protective coatings help preserve your equipment’s quality, making them much easier to resell if needed.
There are Multiple Types of Coating Applications
There are several types of coating applications and materials to use, so you can choose whichever is easiest and most convenient for your company.
Here are two popular methods of application:
Plating
Also known as electroplating, plating is a process that sandwiches metal parts between two metal plates that send a wave of electrons toward the surface, laying out a finish that enhances the surface. Electroplating is used to apply metal protective coatings, and it is a cost-efficient method for application.
Spraying
Spraying industrial equipment delivers better speed and higher-quality finishes, and it is highly versatile. Industrial coating machines work quickly and efficiently to coat your equipment, preparing it for protected use in no time. Instead of using brushes, a sprayer can coat entire equipment sections. The sprayer leaves no stains or marks and dries faster. This process avoids wet paint, meaning you spend less time applying touch-ups and additional finishes.
Additionally, spraying can apply many different kinds of protective coatings, such as resin and powder coatings, as opposed to electroplating, which only applies metal coatings.
When you choose the method that is best for you, just make sure to follow the manufacturer’s instructions for application.
Every Industry Can Benefit
Any industry with manufacturing warehouses can reap the benefits of using protective coatings on their industrial equipment, including yours! You can use protective coating on equipment used in the automotive, food and beverage, and mining industries—among others.
With such versatility and an array of benefits, you should seriously consider protective coating for your industrial equipment. And if you want to invest in protective coating, invest in the best. At your next team meeting, mention the industrial coating machines ArmorLube offers. Our coating equipment enhances your machinery’s performance and quality, and it saves you more money in the long run.
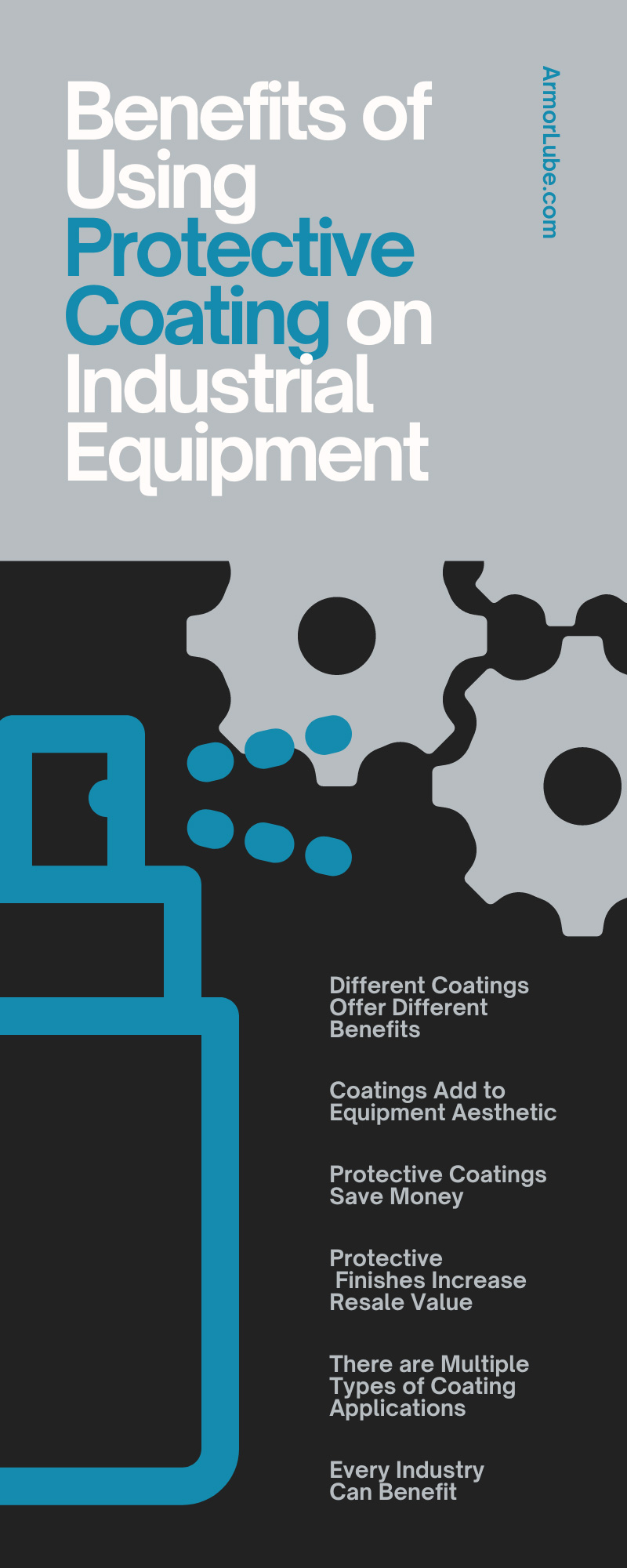