You might not know now, but the pipe coating you have always used once started out as a coal-tar-based mixture that eventually evolved into an abrasion-resistant overcoat for internal pipes. There’s a lot of fascinating insight out there about pipeline coating and how it’s evolved. Since pipe coating has changed over the years, so has the customer service aspect. Find out how pipe coating services have evolved over the years.
How Important Are Pipe Coatings?
We know that pipelines are essential to safely transport energy, but some might not know how crucial coatings are for pipes. The greatest danger to channels is corrosion; if enough builds up over time, it could cause pipes to crack and leak.
You should have pipe coatings to protect your pipes from rusting, especially if they’re buried. Before applying any type of pipe coating, you must consider a buried pipeline’s current state. Pipe coatings are essential to communities and businesses to protect the environment and deliver safer energy, oil, and refined product.
A Brief Look at Pipe Coating Between 1930 and 1950
Pipe coating has been a big topic of discussion lately. The topic has engaged more businesses to think about how their practices affect the surrounding environment, as well as why pipe coating is necessary.
Between 1930 and 1950, the Midwest and some Northeastern states saw a rise in energy demand. Even though energy sources like oil and refineries were bigger in Texas, the Northeast and Midwest noticed that they could benefit from the industries. Despite pipelines benefiting the Northeast and the Midwest, workers in these areas were left wondering how they would get resources to them without transportation by train, boat, or car.
The Development of Pipeline Coatings
Many events occurred between 1930 and 1950, and the use of coatings helped land a historical feat for pipeline transportation. As the pipeline industry grew stronger, technology improved, delivering better ways to supply energy back and forth throughout the country.
Even though energy went back and forth, there was no way for the pipelines to survive, especially being underground. Engineers got to work, experimenting with different things to create a coating system. The best method was using asphalt and coal tar. Over the decade, workers used the coal and tar mixture on buried pipelines, while others used petroleum-based wax.
A Quick Overview of Pipe Coating Between 1950 and 1970
Original pipeline coatings used asphalt, tar, and petroleum-based wax, but that was only a starting point for the future of pipe coatings. In order to ensure that the underground work environment was performing well, workers used hydrocarbon polymers inside the coating products.
Using that same coal-tar-based finisher, coating developers broke down the properties to curate a liquid-based pipeline coating, which we know as epoxy resin today. The reason epoxy was made was to help protect pipes from water, though this process did change over the years.
How Coating Application Methods Changed
At this time, pipe coating makers began developing coating tapes to place around pipes. Workers used coal tar tape on hot pipelines, and once engineers created prefabricated tapes, this was considered cold tape. The tape has adhesives to help it stick to the surface of the pipe. Eventually, the rise of fusion-bonded epoxy in 1960 replaced the earlier versions of pipeline coating systems.
Pipe Coating Types Throughout History
You encounter a lot of pipe coating types that paved the way for what we have today. Take a look at the most interesting pipeline coatings that helped in the evolution of modern pipeline coating systems.
Polyethylene Pipeline Coatings
Polyethylene is the component many coating systems first started with. This coating ingredient is a thermoplastic polymer that softens around pipes when the heat reaches a melting point of 221 to 266 degrees Fahrenheit. Another type of polyethylene pipeline coating is high-density polyethylene (HDPE), typically used with extruded pipeline coatings.
Composite Pipeline Coatings
The next class of pipeline coatings is composite. The composite pipeline coatings were a mix of polymer materials that had better physical properties and resistance to heat, water, and cathodic disbondment. These properties created the composite pipeline coatings class.
Abrasion-Resistant Coatings
The most recent class is abrasion-resistant coatings. These coatings are more commonly used today, second to composite pipeline coatings. The abrasion-resistant coatings give pipelines better protection from abrasion caused by directional boring operations.
Today, you can find three types of abrasion-resistant coating systems: polymer concrete, abrasion-resistant overcoating, and weight coating systems. Polymer concrete is a concrete aggregate and epoxy binder mixture. This mix is used on steel pipes to prevent impact when pulled in a slick-back boring operation.
The abrasion-resistant overcoating protects the pipeline’s base coat from damage. The weight coat is an exterior layer placed on pipelines to prevent negative buoyancy and mechanical parts of pipework in wet environments like swamps, wetlands, and rivers.
How ArmorLube Is Meeting Customer Needs
There’s an even bigger rise in meeting customer needs with coating systems today. At ArmorLube, we spend most of our time researching and developing better, cleaner, and enhanced coating methods to meet customer needs. You can find our workers hard at work finding the best paint finishes that add more protection to pipelines.
Most importantly, we’re developing the next generation of coating services. Our team works nonstop to ensure their knowledge of coating systems helps them answer every client’s question about our methods. Our coating systems are geared to help every industry, especially those working with pipelines. In the same way that pipe coating services have evolved over the years, our services have too.
ArmorLube is here to continue finding the best coating system for your industry. We’re excited to get you started on the best coating method for your company. After contacting us about our internal pipe coating services, you’ll meet a coating specialist who will walk you through the entire process of what our machines do and how they can help you. Contact us today—we’re looking forward to hearing from you!
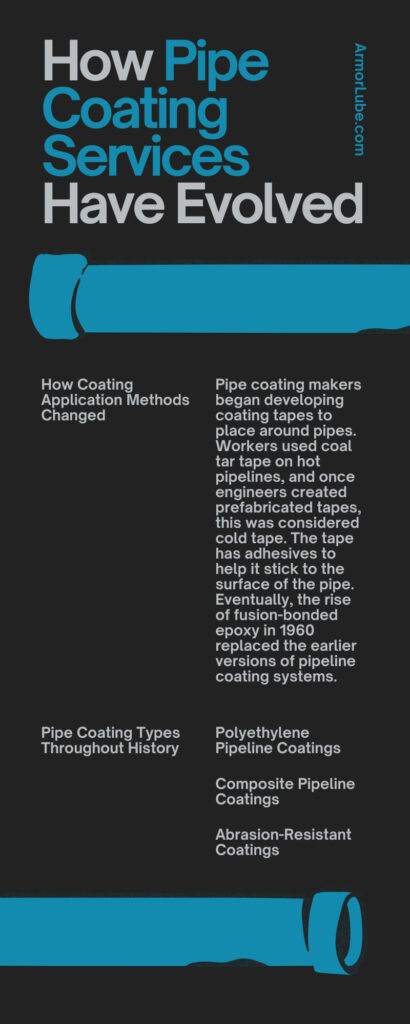